Moisture exists in air in various forms, including solid, liquid and gas. As a result, it's unavoidable that moisture will be generated during the compression process in a compressor. This can pose a problem if left untreated as it can cause damage to the compressed air system and potentially contaminate the end product.
To prevent costly repairs and unnecessary breakdowns, it's crucial to be proactive in maintaining the quality of compressed air. The air must be dry, clean and suitable for the intended application.
There are various types of dryers available, and choosing the right one depends on the required pressure dew-point. Once the air quality has been determined, different technologies can be selected to meet the requirements.
Refrigeration Dryer:
Refrigeration dryers are a crucial component of compressed air systems as they remove moisture from the air, ensuring that it is dry and suitable for the intended application. There are three main types of refrigeration dryers, each with its own advantages and disadvantages.
Direct Expansion Refrigeration Dryers: This type of refrigeration dryer is the most common and stable. It works by continuously cooling the compressed air to 3° Celsius, causing condensation of the water vapor into liquid water. The liquid is then removed through an inbuilt water separator. While this type is reliable, it is also the costliest to operate due to the constant running of the dryer.
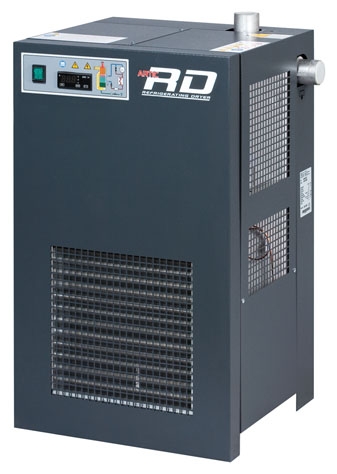
Thermal Mass Refrigeration Dryers: Thermal mass refrigeration dryers use a large mass, such as a water tank or sand, to cool the compressed air. The refrigeration circuit cools the thermal mass, which in turn exchanges heat with the compressed air. This type is energy-efficient as the refrigeration compressor can be turned off once the thermal mass has cooled. However, its efficiency can be affected by fluctuations in the compressed air flow.
Variable Speed Refrigeration Dryer: This type of refrigeration dryer uses inverter technology to adjust the speed of the refrigeration compressor based on the water vapor loading of the incoming compressed air. This results in a more energy-efficient system compared to direct expansion refrigeration dryers. However, the cost and complexity of this type of dryer make it more suitable for larger compressed air flows.
When choosing a refrigeration dryer, it is important to consider the desired dew-point, the compressed air flow, and the energy efficiency of the system. With the right refrigeration dryer, compressed air systems can run smoothly and efficiently, ensuring that the compressed air is dry, clean, and suitable for the intended application.
Membrane Dryer:
A Membrane Dryer is a type of compressed air dryer that uses a permeable membrane to separate the air and water molecules. The compressed air is passed through the membrane, which allows only the air molecules to pass through while retaining the water molecules. This results in a dry compressed air stream that is free of moisture.
Membrane dryers are known for their energy efficiency, as they require no external energy source to operate. They are also compact, low maintenance, and have a long lifespan. Additionally, membrane dryers are capable of producing extremely dry air with low dew points, making them ideal for applications that require a high level of air purity.
However, membrane dryers have some limitations. They are limited in their flow rate and may not be suitable for high-volume air systems. They are also more susceptible to fouling and clogging, which can reduce their efficiency over time.
Overall, membrane dryers are a good option for applications that require a low dew point and high air purity, but they may not be suitable for high-volume air systems. Before choosing a membrane dryer, it is important to consider the specific requirements of the compressed air system, as well as the costs, maintenance, and energy efficiency of the dryer.
Desiccant Dryer:
A Desiccant Dryer is a type of compressed air dryer that removes moisture from the air by using a desiccant material, such as silica gel or molecular sieve. The compressed air is passed through a bed of desiccant, which adsorbs the moisture from the air. The desiccant is then regenerated by exposing it to low-pressure air or by heating it, releasing the moisture and allowing it to be captured for disposal.
Desiccant dryers are known for their ability to produce extremely dry air, even in high humidity conditions. They are commonly used in applications where a low dew point is required, such as in food and beverage processing, pharmaceutical production, and in painting and coating applications.
Desiccant dryers come in two main types: heatless and heated. Heatless desiccant dryers regenerate the desiccant by exposing it to low-pressure air, while heated desiccant dryers regenerate the desiccant by heating it. Heated desiccant dryers are typically more efficient and faster than heatless dryers, but they are also more expensive and consume more energy.
Desiccant dryers require regular maintenance, as the desiccant bed needs to be changed periodically, and the unit may need to be cleaned regularly to maintain its efficiency. Additionally, desiccant dryers are relatively large and require a significant amount of floor space.
Overall, desiccant dryers are a good option for applications that require a low dew point and high air purity, but they may not be suitable for energy-conscious or cost-sensitive operations. Before choosing a desiccant dryer, it is important to consider the specific requirements of the compressed air system, as well as the costs, maintenance, and energy efficiency of the dryer.
Integrated Dryer:
An Integrated Dryer is a type of compressed air dryer that combines the functions of a compressor, air filter, and dryer into a single unit. This integrated design helps to save space, reduce installation costs, and simplify the operation and maintenance of the compressed air system.
Integrated dryers come in a variety of configurations, including refrigerated, desiccant, and membrane dryers. Depending on the specific type of integrated dryer, it may use a combination of technologies, such as cooling and adsorption, to remove moisture from the air.
Integrated dryers are typically used in small to medium-sized compressed air systems, where space is limited, and ease of use is a priority. They are often used in a variety of applications, including workshops, garages, and laboratories.
One of the main benefits of an integrated dryer is that it simplifies the installation and operation of the compressed air system, as all the components are integrated into a single unit. This helps to reduce the number of components, which can make the system more reliable and easier to maintain.
However, it is important to note that integrated dryers may not be suitable for larger or more demanding compressed air systems. The capacity of the dryer may be limited, and the unit may not be able to provide the same level of air quality and efficiency as a standalone dryer. Additionally, if the integrated dryer fails, it can be more difficult and expensive to repair than a standalone dryer.
Before choosing an integrated dryer, it is important to consider the specific requirements of the compressed air system, as well as the costs, maintenance, and energy efficiency of the dryer. It is also important to consider the benefits of having a more flexible and scalable system that can be easily expanded or upgraded, as this may be a more cost-effective solution in the long term.