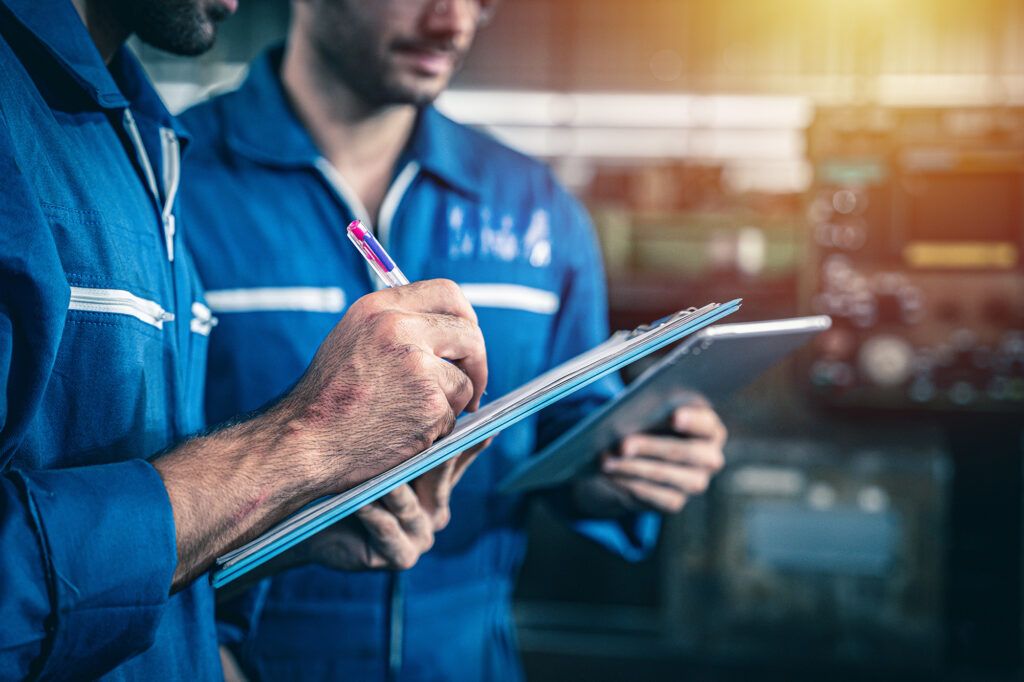
Air compressors are a vital component of many industrial processes, providing compressed air to power tools, equipment, and systems. However, air compressors can also consume a significant amount of energy, making it essential to optimise their efficiency to minimise costs and reduce environmental impact.
In this blog post, we’ll discuss seven essential tips for optimising your air compressor’s energy efficiency, helping you save money and operate more sustainably.
-
- Regular Maintenance and Inspection
One of the most crucial factors in maintaining an energy-efficient air compressor is regular maintenance and inspection. Routine servicing, including changing oil, filters, and belts, helps ensure that your compressor operates at peak performance. Inspecting your air compressor system for leaks, pressure drops, and other issues can also identify potential inefficiencies that may be wasting energy.
Some maintenance tasks to perform regularly include:
-
- Cleaning and replacing air filters to reduce pressure drop and ensure optimal air intake
-
- Checking and adjusting belt tension to minimise energy loss through slippage
-
- Lubricating moving parts to reduce friction and wear, which can decrease efficiency
-
- Inspecting and repairing any leaks in the compressed air system
-
- Proper Sizing of Your Air Compressor
Selecting the right size air compressor for your specific needs is crucial for energy efficiency. An undersized compressor will work harder and consume more energy to meet demand, while an oversized compressor will cycle on and off more frequently, wasting energy and causing unnecessary wear.
When sizing your air compressor, consider factors such as your facility’s air demand, pressure requirements, and the types of tools and equipment you’ll be using. Consulting with an experienced compressed air professional, like the team at Airmech, can help you determine the appropriate size and type of air compressor for your needs.
-
- Use Variable Speed Drives (VSDs)
Variable speed drives (VSDs), also known as variable frequency drives (VFDs), can significantly improve the energy efficiency of your air compressor system. VSDs adjust the motor speed based on demand, ensuring that the compressor only produces the required amount of compressed air at any given time.
By using a VSD, you can reduce energy consumption by up to 35% compared to a fixed-speed compressor. Additionally, VSDs can lower maintenance costs and extend the lifespan of your compressor by reducing wear and tear associated with frequent start-ups and stops.
-
- Implement an Energy Management System
An energy management system (EMS) is a software-based tool that can help you monitor, analyse, and optimise the energy usage of your air compressor system. EMS can track key performance indicators (KPIs), such as power consumption, pressure, and flow, enabling you to identify inefficiencies and make informed decisions about system adjustments or upgrades.
By using an EMS, you can gain a better understanding of your air compressor’s energy usage patterns and develop strategies to minimise waste, such as adjusting operating schedules, optimising maintenance routines, or upgrading to more energy-efficient equipment.
-
- Optimise Compressed Air Distribution
The design and layout of your compressed air distribution system can have a significant impact on energy efficiency. Minimising pressure drops, avoiding sharp bends, and using properly sized pipes can all contribute to a more efficient system.
Consider the following tips for optimising your compressed air distribution system:
-
- Use larger diameter pipes to reduce pressure drop and friction
-
- Install pressure regulators at points of use to minimise pressure fluctuations
-
- Eliminate unnecessary bends and turns in pipework to reduce pressure loss
-
- Regularly inspect and maintain distribution system components, such as valves, fittings, and hoses, to prevent leaks and ensure proper function
-
- Recover and Reuse Waste Heat
A significant amount of energy used by an air compressor is converted into waste heat, which is typically expelled into the environment. By implementing a heat recovery system, you can capture and reuse this waste heat, providing an additional energy-saving opportunity.
- Recover and Reuse Waste Heat
Heat recovery systems can be used for various purposes, such as preheating water for boilers or heating spaces within your facility. Some air compressors even come with integrated heat recovery options, making the process more straightforward.
To determine the feasibility of a heat recovery system for your air compressor, consider factors such as the size and type of your compressor, the amount of waste heat generated, and potential applications for the recovered heat within your facility.
-
- Conduct Regular Energy Efficiency Audits
Regular energy efficiency audits can help you identify inefficiencies in your air compressor system and develop strategies to improve performance. An audit typically involves analysing system performance data, inspecting equipment and distribution systems, and evaluating maintenance practices.
By conducting energy efficiency audits, you can uncover opportunities for improvement, such as upgrading equipment, optimising distribution systems, or adjusting operating procedures. Regular audits can also help you track the effectiveness of your energy-saving initiatives and make adjustments as needed to maximise efficiency.
Optimising your air compressor’s energy efficiency is an essential aspect of managing your facility’s overall energy consumption and costs. By implementing these seven essential tips, you can improve the performance and lifespan of your air compressor system, reduce energy waste, and contribute to a more sustainable operation. At Airmech, our team of experts is dedicated to helping you find the best solutions for your compressed air needs. Whether it’s selecting the right air compressor, conducting energy efficiency audits, or providing ongoing maintenance and support, we’re here to help you maximise efficiency and minimise costs. Contact us today to learn more about our comprehensive range of compressed air services.